Built up Roof (BUR) – What is it?
First let’s go back into history and see why and what Built Up Roofing is. I can attest that I know, as a young child, when I was working for my family’s contracting company, that when we installed a built-up roof, I was pretty sure that I was working on the doorsteps of hell – especially if we were installing a system that had coal tar “pitch.” I can pretty much tell you that hell was probably a better place to be then working with that product. It was absolutely brutal, and it burned you to the bone. Installing a built-up roof is hard work. It quickly separates the men from the boys. It’s hot, dangerous work, and it makes me quite happy that I’m not having to work like that today.
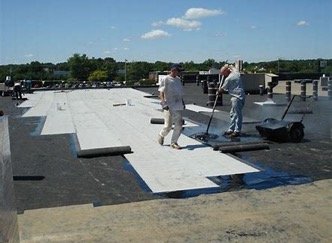
I’m not quite sure how Moses dealt with that while building the Ark, but perhaps it was just a thick crude oil that made the boat watertight.
The History of Built-up Roofing
According to a RCI-online.org article from September 2009 “Built-Up Roofing: an Historic Perspective,” by Carter Slusher, as he offers a fair historic overview, writing that:
“In the late 1800s, BUR materials were used to replace lead sheets on commercial wooden buildings.
BURs were constructed in situ, using alternating layers of jute and tar or lake asphalt. These constructions, though crude, used largely unrefined bitumen that was rich in natural constituents and provided an improvement over conventional roof constructions of the time. Documented use of asphalt for roofing, in preference to coal tar, began in the 1870s. However, its use became prevalent as petroleum refining technology improved in the early twentieth century. Asphalt gained preference because it was easier to handle and had a wider functional temperature range than coal tar.”
I’ve got to tell you, I’m pretty disappointed by the articles I’ve read about built-up systems, and what it is, and its history. And I certainly get it. It’s not a very interesting subject. However, one can quickly glean that the authors (of articles I read through) have never had any applicable experience, as is the case with most roof installers today. The above article may certainly be a fair or logical understanding of how BUR started to evolve and why. There’s certainly no reason that I can see to disagree. Beyond that you’re going to get my perspective.
First. What is a built-up roof? A BUR is a roof assembly or layers of fiberglass, organic, or modified membranes(felts) that have been cemented together by a bituminous product such as type3, or 4 hot asphalt, cold applied adhesive, or perhaps coal tar pitch. The roof is then completed by, either a flood coat of asphalt, a gravel or ballast application, or a reflective coating.
Advantages and Disadvantages of Built-Up Roofing (BUR)
It’s a fabulous system when properly installed. Today most roofers do not even have the slightest bit of knowledge about these type of assemblies.
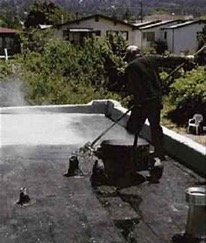
The pros:
- Will typically go beyond its intended life cycle, with proper roof maintenance.
- Works well in almost all environments.
- Esthetically pleasing
The Cons:
- Costly to install today. Labor and equipment intensive. Expect to pay $800-$2000 per square
- Properly trained installers are few and far between.
- Has been considered highly carcinogenic and fumes emit strong odors.
What are the most important factors of a BUR?
Here are a few things to consider.
The use of proper material. Materials that perform similarly and are intended for use in built-up roofing.
The Details
The absolute most important thing when installing a built roof are the details. Get these wrong, and you can expect have a premature failure along with a lot of headaches and interior damage.
So, what are some typically details?
- First – Fastening of sub-membrane items I.e. roof deck, roof insulation, etc.
- Second – the temperature of the bitumen. This is critical!
- Third – Termination or transition points.
- Fourth – protrusions. Proper sheet metal roof flashing and the use of asphalt primer on all metal that touches the membrane.
One last thing is weather conditions. BUR systems are extremely volatile to moisture during installation. Appropriate planning and forecasting should be considered. Moisture introduced during the construction phase will surely cause performance issues down the road. If you’re a contractor, the weather can absolutely and directly affect your cash flow.
BUR is more than just layered felts, finished with a layer tar and gravel. Today’s more popular built up systems are modified membranes used in conjunction with sebs asphalt. These modified
products can be assembled by using hot asphalt, adhesives, torch and now peel and stick. Technology still plows ahead to improve these products.
Built up systems are typically used on higher end commercial building projects. It would not be
uncommon to find some form of a built-up or hybrid roof on schools, hospitals, government buildings and high-end private facilities. A properly installed built up commercial roof can last well into 30 years, and with the introduction of liquid applied solutions, I expect to see numbers double in the near future.
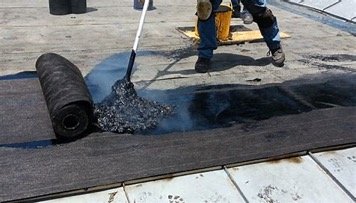
Today’s architects, engineers and roofing inspectors have such great flexibility in designing roofs that can basically stand up to anything you throw at it. Having an ability to combine hot applied, cold applied built up roofing with today’s great single ply roof systems like EPDM, TPO, and PVC, is short of amazing. As I see it, the only two things that prohibit a “perfect” roof are your budget and today’s workforce, with the latter being more worrisome.
In closing, no matter which way you decide to go, always use uniform roofing products from the same manufacturer. This is easily verified. And always use a contractor that you trust. A good commercial roofing contractor will have been around for some time. Besides, it shouldn’t ever be about the money. It should be about the relationship. Your roofer is your partner, and when you need that partner to show up, you need to know that they’re going to be there.
If you have a flat roof and you need roof consulting, roof inspection or an evaluation, then feel free to give us a call. Cook Roofing Company is a family-owned-and-operated commercial roofing company that has been around since 1913! We’ve been providing commercial roofing services in cities across the Midwest like Springfield and Branson, MO for over 100 years and have enjoyed being of service to our clients. Although the industry has changed over time, we’ve kept on top of the latest roofing tools, practices, roofing materials, and techniques.
That’s why we’ve made a point in providing a lifetime workmanship warranty for all of the work we perform on your property. We are one of the few businesses nationally that offer a warranty like this, so take advantage in selecting Cook Roofing Company as your chosen roofing company. We’re confident that you’ll be satisfied with your end results.
Below is a list of manufacturers for BUR products:
For more information, see these pages: