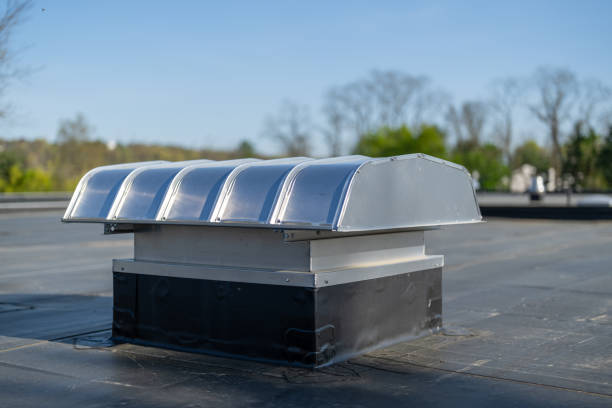
What about EPDM Roofing Systems?
EPDM is a highly durable, flat and low slope roof covering made from synthetic rubber. EPDM stands for Ethylene Propylene Diene Monomer. It’s a single-ply rubber roofing membrane that consists of a carbon synthetic rubber. EPDM has been used on commercial roofing facilities since the early 1960s and is now considered a proven, quality roofing option. EPDM roofing products have a time-proven history with commercial roofin. Despite this, however, it only has about 12-15% of the commercial roofing market.
EPDM allows you several thickness options to choose from: 45, 60, or 90 mils thickness, and can even be fleece backed. Colors are limited to black and white. Other single ply roofing systems, such as TPO and PVC, have a natural white color. EPDM ages well, and color typically will not fade, other than by dust and debris. Proper roof maintenance will keep your single-ply roof color looking new.
Expert EPDM Roofing Installation Services by Cook Roofing CO.
EPDM roofing can be installed using a few different methods – mechanically attached, fully adhered, or ballasted (with gravel on top). The seams of the material are sealed with special tape or liquid adhesives.
To the layman, EPDM roof material will quickly remind you of a huge inner tube from a vehicle. It’s what we used to float the creek on when I was a kid. It was always a great day to go to the MFA tire center and get a patched truck or tractor tire to go float on. What great memories!
Applications
EPDM roofing systems are typically used on large commercial properties. One reason for this is that most EPDM roofs were installed in a way that allowed for the roofing membrane to be loosely laid over unfastened insulation and then weighted down by a large rock to create a ballasted roof system. The use of the rock as a ballast really only served one purpose, and that was weight, it was only years later that the rock was determined to be a great UV protection because it absorbed damaging sun and was highly reflective.
Considerations
To understand what a commercial roofing system is, we need to understand what is expected out of a roof besides shedding water. There are many factors that go into that decision-making process. Here are just a few:
- Does the roof need to have fire resistance?
- Will the roof system go on a sloped roof or a pitched roof?
- What kind of roof maintenance will be required?
These are just a few questions, and as you can see, your questions need to be thorough and specific when deciding the commercial roofing system on your building. A good commercial roofing contractor can guide you and help you to determine the best roofing solution for you.
Why would I consider an EPDM roof? Really, the only reason would be for the ease of installation. To compare EPDM against another single ply roofing system such as TPO and PVC roofing systems. They are all pretty much and equal with little differences. The key to any commercial roofing system lasting is ongoing roof inspections. The proper use and application of these type of roofing materials is paramount to longevity and duration of any roof.
Today all new roofing systems, from the new type of built up roofs (BUR) with tar and gravel to a new and improved modified bitumen roofs, along with the underlying roof insulation, must adhere and comply to energy efficient standards as set out by the (IECC) International Energy Conservation Code. There are guidelines for commercial and residential roofing that must be met. Further information can be found at www.energycodes.gov.
Here are my thoughts on EPDM… I can remember as a young roofer, when EPDM was starting to get traction in the industry. I was brought up and trained on flat roofs that were always tar and gravel. This type of built up roof (BUR) was slow to install, and at the end of the day was a painful way to make a living. And, as if that was not enough, you got up the next day and did it again…. So, getting back to EPDM… this rubber roofing today is as good as or equal to any other roofing assembly available. What makes any roof worth its weight is always using quality products and installing them the way that the manufacturer suggests.
Common uses for EPDM roofs are on big box stores and large warehouse facilities. What made this roof so popular was that the entire roofing system could be installed “Loose” – meaning that the roof insulation under the roof membrane and the EPDM could be installed in one monolithic way. Only the seams and roof protrusions would need to be flashed. Other than that, the rock ballast applied around 1,200 lbs per square (100 square feet), and that was what held the roof assembly in place. This was a plus for a commercial roofing company and a building owner or developer, since a lot of roof could be installed in a day’s time, and made watertight. Not only did this mean more money in profit to the installer, it also meant saving money for the customer. So, production and ease of installation are what really allowed all single-ply roofs to get heavily rooted.
Now, the downside to a ballasted roof was leaks. And wow, when there are leaks, they are not particularly easy to find! First, all the rock in the area where the leak is has to be removed. This often causes more leaks, because the ballast is too big to sweep with a broom, you must use a shovel or other mechanical device to move the rock. This often creates roof punctures that don’t show up until the next rain. The other, and most obvious problem, is the extreme weight. For instance, a Super Kmart or Super Walmart are both around 180,000 square feet. Not considering the membrane, insulation, and other mechanical equipment, such as skylights, and HVAC – just the roof ballast by itself would weigh around 2 million pounds. That’s a lot of stress on a building structure.
So, by bad design or a clogged roof drain, or perhaps a tornado or heavy snow, that weight in some instances became too heavy, resulting in roof cave in or roof collapse. Because of this, application techniques needed to change. What came out of it, is what is used today in nearly all single roof applications. Mechanically attached and fully adhered single ply roofing. Obviously, fully adhered means fully glued to a substructure of some kind – i.e. roof insulation, gypsum decking, etc. Mechanically attached that all seams would be fastened to the roof structure.
To make a long story short, every single ply roof used today evolved from EPDM methodologies. The failures, the wins, the applications. As an old roofer I do have a great appreciation for EPDM, and when I install roofs on my commercial properties I always go toward the use of and EPDM before all other roofing systems.
Cook Roofing Company is a family-owned-and-operated roofing company that has been around since 1913! We’ve been providing roofing services in cities across the Midwest like Springfield MO and Branson for over 100 years and have enjoyed being of service to our clients. Although the industry has changed over time, we’ve kept on top of the latest tools, practices, roofing materials, and techniques.
That’s why we’ve made a point in providing a lifetime workmanship warranty for all of the work we perform on your property. We are one of the few businesses nationally that offer a warranty like this, so take advantage in selecting Cook Roofing Company as your chosen roofing company. We’re confident that you’ll be satisfied with your end results.
If you’re looking for more information about EPDM roofing material and more from the manufacturers, then we recommend you look at the following companies.
- Firestone Building Corp. www.firestonebpco.com
- Carlisle Syntec www.carlislesyntec.com
- Johns Manville www.jm.com